Foam Formation and Control in Shake Flask Bioprocessing
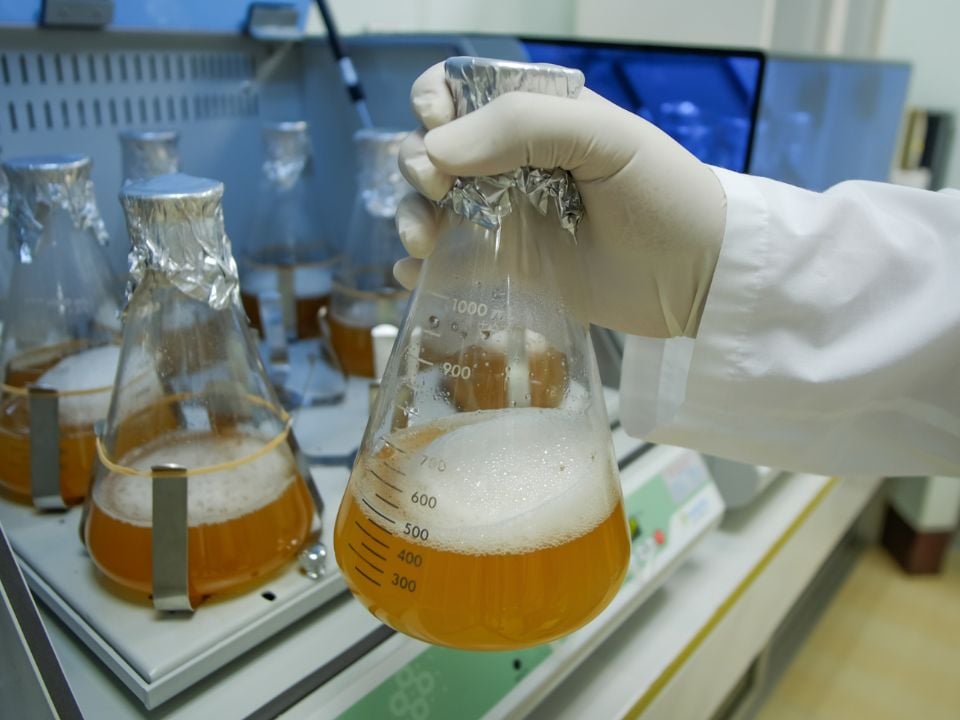
While a common sight in bioprocessing, foam is considered an industry-wide problem and can have a significant impact on cell growth, product yield, and overall process efficiency. In this post, we will jump into the world of foam, exploring its causes, consequences, and potential solutions.
Understanding Foam
Foam is defined as a complex honeycomb structure composed of gas pockets separated by liquid membranes and forms at the interface between the liquid and gas phase in a culture vessel. When these individual bubbles accumulate faster than they can decay, we refer to this as foaming. Commonly seen in larger stirred vessel types and shake flasks, foaming is a challenge that has few great solutions.
The Problem with Foam
There are some key concerns when dealing with foam in bioprocessing. The primary problem is while a thin foam layer can help with oxygen transfer as the surface-area-to-volume ratio increases, at a certain point, a thick foam layer will act as a gas barrier. Lower oxygen transfer rates can lead to reduced cell growth, and thus lower product yields. Foam formation can reduce the effective working volume your shake flask by displacing liquid volume. This decreases the overall productivity of the bioprocess as less space is available for microbial growth and metabolite production.
Another issue when dealing with foam is that cells can become trapped in the bubbles or adhere to the vessel walls. When this happens, certain measurements, such as biomass, may no longer be accurate. Additionally, as bubbles burst, cells can become damaged, further impacting your bioprocess.
Causes of Foaming in Bioprocessing
Identifying the factors contributing to foaming is crucial for optimizing bioprocesses.
- Agitation and Aeration
Many microorganisms require oxygen to support metabolic activities and growth. In order to achieve increased cell densities and thus greater product yields, most bioprocesses require an increase in oxygen demands. For this to happen, agitation and aerations rates must also increase. This is often achieved by increasing the shaking speed in the shaker. These higher speeds can result in the generation of foam as gas bubbles are introduced into the medium. Finding the right agitation speed is crucial for preventing excessive froth.
When working in shake flasks, specifically, we often see the use of baffles as a means to improve aeration. However, with baffles comes a higher risk of foam formation which may impede oxygen transfer. Learn more about baffled versus non-baffled flasks here! - Microbial Growth
While agitation and aeration are a common source of foam formation, it is not the only reason. As cell density increases, the production of extracellular compounds like proteins and polysaccharides rises, contributing to foam formation. - Surfactant Production
Some microorganisms naturally produce surfactants. These biologically derived surfactants (or biosurfactants) reduce surface tension and facilitate the formation of stable foam. - Medium Composition
The choice of culture medium and its components can influence foaming. More often seen in complex media, certain nutrients or additives may exacerbate foam formation. - Temperature and pH
Variations in temperature and pH, two important bioprocessing parameters, can affect microbial growth.
Combatting Foam in Your Bioprocess
Overall, foam formation in bioprocesses can negatively impact process performance, product quality, and operational efficiency. Therefore, effective foam control strategies are essential for the successful operation of bioprocessing systems.
Larger vessels, such as stainless-steel bioreactors, have mechanical foam breakers built into the headspace. Unfortunately, these options are not available in smaller bioreactors or shake flasks, so chemical methods are typically used. These chemical agents are called antifoams and are designed to prevent the formation of foam by reducing the surface tension of the liquid medium. There are several types of antifoam agents commonly used in bioprocessing, each with its own characteristics and suitability for specific applications:
- Silicone-based Antifoams: Silicone-based antifoams are among the most commonly used antifoam agents in bioprocessing. They are effective at breaking down surface tension and destabilizing foam bubbles. Silicone-based antifoams are generally stable over a wide range of pH and temperature conditions, making them versatile for various bioprocessing applications.
- Mineral Oil-based Antifoams: Mineral oil-based antifoams are another category commonly used in bioprocessing. They work by coating the surface of foam bubbles, preventing them from coalescing and stabilizing. Mineral oil-based antifoams are often preferred for applications where silicone contamination is a concern, such as in pharmaceutical or food processing.
- Polymer-based Antifoams: Polymer-based antifoams function by adsorbing onto the surface of foam bubbles, disrupting their stability. These antifoams are often used in bioprocessing applications where silicone or mineral oil contamination is undesirable. Polymer-based antifoams can be tailored for specific applications by adjusting their molecular weight and chemical composition.
- Vegetable Oil-based Antifoams: Vegetable oil-based antifoams are derived from natural sources such as soybean or corn oil. They are often used in bioprocessing applications where environmental sustainability or biodegradability is a concern. Vegetable oil-based antifoams can provide effective foam control while minimizing the environmental impact of the process.
- Non-silicone Antifoams: Non-silicone antifoams encompass a variety of compounds that do not contain silicone as the active ingredient. These antifoams may include organic compounds, fatty acids, or other surfactants. Non-silicone antifoams are chosen for applications where silicone contamination is a concern, or when specific regulatory requirements mandate the avoidance of silicone-based additives.
- Biodegradable Antifoams: Biodegradable antifoams are designed to break down naturally in the environment, reducing their environmental impact after use. These antifoams may be based on renewable resources or biodegradable polymers. Biodegradable antifoams are increasingly preferred in bioprocessing applications where sustainability is a priority.
The choice of antifoam depends on various factors including the specific requirements of the bioprocessing application, compatibility with the process and product, regulatory considerations, and environmental concerns. While antifoaming agents exist as a solution to limit foam formation, there are potential adverse effects as well, and it is important to carefully select the appropriate antifoam agent to ensure effective foam control without compromising process efficiency or product quality.