SBI Chosen by Sudhin Biopharma to Collaborate on Advanced Regenerative Manufacturing Institute Award-Funded Project
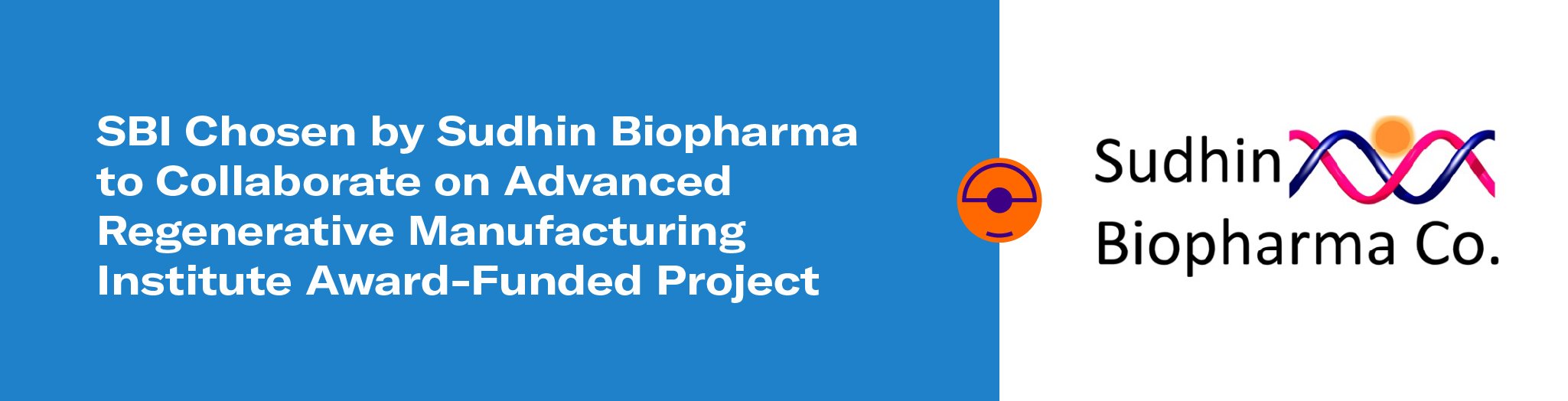
Sudhin Biopharma (Sudhin), a biotechnology company that develops efficient, continuous biological manufacturing processes for biologic therapeutics and viral vaccines, has selected Scientific Bioprocessing, Inc. (SBI) as one of its partners in a collaborative project recently selected for funding by Advanced Regenerative Manufacturing Institute (ARMI). ARMI is a non-profit consortium of leading life science companies, academic institutions, non-profit organizations and key thought leaders working to realize the vast, yet unrealized promise of tissue engineering and regenerative medicine (TERM).
SBI will deploy its optical sensing technology to provide real time dissolved oxygen (DO) and pH monitoring capabilities within Sudhin’s BioSettler technology.
“We are honored to be partnering with Dr. Kompala, the Sudhin Biopharma team and Pluristyx on this ARMI project. Sudhin’s BioSettler technology and our advanced optical sensing products can create an ideal cell culture environment that can be sustained across all parts of the development process. Together, we can leverage our mutual capabilities and knowledge-base to increase cell culture efficiency and productivity, while reducing time to market and what it costs to deliver therapeutics to patients,” stated SBI’s President John Moore.
Sudhin is located in Boulder, Colorado and was founded in 2014 by Dr. Dhinakar Kompala. The company’s technologies include inclined, novel, compact, and single-use BioSettlers. Sudhin’s core focus is on the separation of cells and particles by exploiting their different sedimentary velocities, which enables the removal of dead cells and the recycling of viable cells back into the bioreactor. Sudhin’s BioSettler products are designed to achieve high cell viabilities and enhanced bioreactor productivity.
Pluristyx, Inc. of Seattle, Washington has also joined the team to investigate a scaled-down version of the BioSettler to retain pluripotent stem cell clusters inside its cell expansion bioreactor cultures while adding new cell culture media and removing spent media daily.
Sudhin is seeking to expand the potential applications of its BioSettler through this ARMI-funded project with the deployment of SBI’s optical sensors to provide real time monitoring of key cell conditions. Using a controlled gas mix of O2, CO2 and air sparged through the cell culture media inside the BioSettler, Sudhin plans to enable cell growth inside the novel Integrated Settler Bioreactor and harvest selectively the concentrated cells at its bottom or the clarified supernatant at its top.
Such an Integrated Settler Bioreactor (ISB) can have many novel applications in stem cell growth and differentiation protocols. Another ARMI partner is currently interested in the ISB to grow neuronal stem cells and harvest exosomes, for example. Exosomes have molecules that can direct them to a specific location in the body, cross the blood-brain barrier and deliver their RNA, DNA, antibodies or other therapeutic protein cargo to treat seemingly intractable diseases like Alzheimer’s and Parkinson’s.
Currently, mesenchymal or neuronal stem cells are grown attached to the plastic surfaces on stacks of tissue culture flasks, which are mostly kept inside a CO2 incubator where pH and temperature are controlled, and then taken regularly to biosafety cabinets to exchange media. The stem cell expansion process as it is practiced currently moves the cells on stacks back and forth between the incubator and biosafety cabinet, is invasive, and is highly labor intensive.
“If we can measure pH and DO in my settler, I can determine if they are in acceptable life supporting ranges. If they deviate, what can we do about them? Maybe we strip the CO2 from the liquid, or we can add some CO2 bubbles to control the pH to bring it into range,” stated Dr. Kompala. “SBI’s sensors provide us the capability to monitor these key indicators in real-time, giving our team the opportunity to make adjustments in the sparged gas mix to create and maintain an ideal cell growth environment.”
“If we can measure and control pH and DO in the settler, we no longer need the incubator; we no longer need to take it to a biosafety cabinet because our table-top settler is a closed device, from which we can pump in fresh cell culture media and remove spent media at any desired rate, continuously or intermittently. This process is more controllable and highly scalable. We think this ARMI collaboration will produce a highly versatile ‘Intelligent Settling Bioreactor’ or ISB, which is what John Moore has called this potential technology,” he added.
Sudhin’s ARMI project will move through four six-month phases. At the end of the first six months, collaborators should know if they can not only measure pH and DO, but also control pH and DO levels. If all goes well, Sudhin hopes to demonstrate mammalian cell growth and selective harvesting protocols in an ISB prototype within 24 months.
“We’re happy to work with a company connected with the original inventor of optical sensors, Dr. Govind Rao, the Director of CAST at UMBC and Pluristyx. Our collaboration with SBI is just beginning, but I’m very happy to have connected with the SBI team. They are all very experienced people in sensor technology and I’m excited to learn something from them and teach them what I know,” stated Dr. Kompala.
“This is a terrific opportunity to showcase the power of our sensing technology and to make a valuable contribution not only to Sudhin’s efforts to develop its Intelligent Settler Bioreactor, but also to the advancement of cell culture reproducibility, consistency and productivity,” added Moore. “This is a coupling of terrific technologies and experienced, deep teams that have the potential to vastly improve cell culture performance for cell and gene therapy, tissue engineering and biotech and biopharma applications. We’re excited to be part of the ARMI consortium and to contribute to this project and ARMI’s wider mission.”