SBI and the ARMI Partner Network on a Mission to Realize Tissue Engineering’s Promise
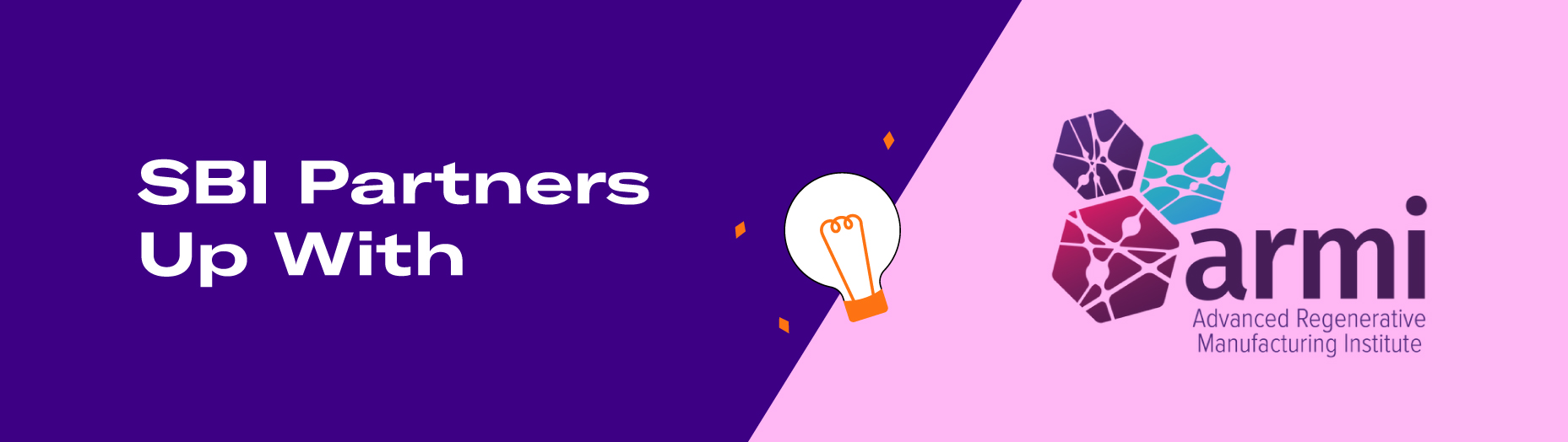
The Advanced Regenerative Manufacturing Institute (ARMI) is a non-profit consortium of leading life science companies, academic institutions, non-profit organizations and key thought leaders working to realize the vast, yet unrealized promise of tissue engineering and regenerative medicine (TERM).
Scientific Bioprocessing, Inc. (SBI) is proud to be part of the ARMI partner network. SBI is contributing its sensor technology and bioprocessing expertise to several ongoing BioFabUSA projects focused on the automation and scale up of tissue manufacturing, which are major obstacles to the field’s commercial viability and more widespread utilization.
“SBI is aligned with our philosophy. John Moore and the SBI team bring thought leadership that focuses on the future. They understand the only way the industry can move forward is through closed systems and good measurement that can work hand-in-hand with those systems,” stated Tom Bollenbach, ARMI’s Chief Technology Officer.
“We are extremely excited to be contributing to the great work being done by ARMI’s BioFabUSA and its partners. We hope that by lending our technology and bioprocessing expertise to various projects and working groups we can help automate, scale up and streamline tissue manufacturing to ultimately deliver on its promise to researchers and patients in need,” stated John Moore, SBI’s President.
“Tissue engineering is an industry that has been in perpetual transition between R&D and commercialization for its entire existence. In 1976, Dr. Eugene Bell at MIT published a paper on the production of living skin. By the end of the 1990s, Scientific American wrote about the promise of tissue engineering, but this never materialized,” stated Bollenbach.
“Between 2012 and 2014 the DoD, NIH, and NSF funded nearly $3B in basic tissue engineering R&D, yet there is still no product. What people now realize is that the problem is one of scale and manufacturing. These are the bottlenecks,” he added.
ARMI’s BioFabUSA, which was founded in 2017 with the support of $80M in funding from the Department of Defense (DoD), is on a mission to remove tissue commercialization bottlenecks by making practical the scalable, consistent and cost-effective manufacturing of engineered tissues and tissue-related technologies. BioFabUSA’s work includes innovations across five focus areas: (1) Cell Selection, Culture and Scale-up, (2) Biomaterial Selection and Scale-up; (3) Tissue Process Automation and Monitoring; (4) Tissue Maturing Technologies and (5) Tissue Preservation and Transport.
“We are trying to address scalability, consistency and cost. You can make tissues right now, but it is all artisanal. It’s technicians in a clean room using the tools of the scientist and not the engineer. This keeps cost high because of all the labor involved,” shared Bollenbach.
BioFabUSA is running 25 active projects that align with gaps identified in the tissue biomanufacturing process. Five more projects will be coming online in the near future. These projects are focused on standardizing and stabilizing cell media, developing equipment that makes the cell the medicine, increasing automation through machine learning, improving transportation, storage and preservation techniques and developing high throughput screening techniques to better understand if a tissue will actually function for a patient.
Underpinning all of these important initiatives is the need to measure the right variables, collect the right data and better understand the tissue engineering process in real time.
“We use the phrase SMAC at our Tissue Foundry, which means Scalable, Modular, Automated, and Closed. We are driving a hard line to closed manufacturing systems. SBI is a key part of this. The measurement technology they have developed is highly compatible with closed manufacturing,” stated Bollenbach.
“SBI is involved in a collaborative project with an academic partner to measure dissolved oxygen, pH, glucose and lactate by integrating their sensors with bioreactors and other cell culture systems to provide real-time, in-line monitoring of cell attributes. SBI is also providing ARMI members with sensor kits and helping these members to integrate sensors into their respective systems,” he added.
The creation of modular, automated, closed, standardized and scalable tissue engineering and manufacturing will lead to increased product commercialization and availability to researchers and patients in need. Streamlined processes will reduce costs to the companies manufacturing tissues, organs-on-a-chip and organs; it will benefit researchers by enabling them to run toxicity tests on organs grown in the lab; it will improve diagnostic testing; and it can be deployed to restore form, function and appearance to wounded soldiers and other patients, for example.
“SBI’s closed, non-invasive, real-time sensors are just massive for us. We want to generate a lot of data; the ability to collect large amounts of data is the future of this industry. This is what SBI’s technology and expertise will empower us to do,” shared Bollenbach.