
Overview
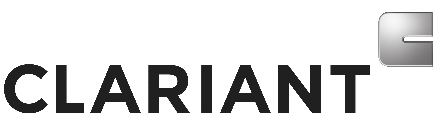
Key Facts
Location: 110 operating companies in 53 countries
Headquarter: Muttenz (Switzerland)
Employees: approx. 11 500
Focus: Key trends of our time, including energy efficiency, renewable raw materials, emission-free mobility, and conserving finite resources.
Clariant addresses trends for safe and sustainable chemistry
Clariant is one of the world’s leading specialty chemical companies, headquartered in Muttenz (Switzerland). It offers innovative and sustainable solutions for very specific needs of customers from various industries. Addressing the key trends of our time, spanning from energy efficiency to emission-free mobility, Clariant’s portfolio derives from three business areas:
- Care Chemicals
- Natural Resources
- Catalysis
With the help of modern biotechnology, bio-based products are manufactured as alternatives to fossil-based chemicals. To achieve this, Clariant uses several microorganisms as workhorses, including strains of the bacterium Bacillus spec.
While microbial protein production is ultimately often carried out in large scale bioreactors, upstream experiments to investigate ideal conditions or select the optimal production strain are preferably performed in shake flasks. These small-scale vessels enable low-cost tests due to reduced medium and nutrient quantities used, and because they are easier to set up than bioreactors, the experiments save time and labor costs.
However, shake flasks usually lack the advanced control options that bioreactors can offer. The continuous or discontinuous feeding of substrate, for example, is routinely used in bioreactor experiments, enabling e.g., fed-batch cultivations. In shake flasks these advanced feeding options are an exception and shake flask experiments usually only offer batch cultures.
Drawbacks of Testing Production Strains in Batch Cultivations
Production of unwanted by-products
Acidification of the medium
Altered cell physiology and cell lysis
Physiological changes impede the analysis of production behavior
Dr. Kambiz Morabbi Heravi, strain engineer at Clariant, encountered diverse drawbacks when using shake flask batch cultures to test different production strains of Bacillus spec. With the entire carbon source concentration presented to the cells from the beginning of the cultivation, they rapidly reached the stationary phase due to the carbon overflow metabolic pathway. The high rate of substrate metabolism presumably led to the undesired production of by-products that acidified the medium. Visibly, the suboptimal conditions led to a changed cell physiology and even cell lysis in later stages.
Because of the great impact on the cell’s metabolism, the effect of the batch process overshadowed the strains characteristic biomass and protein production behavior. Therefore, these pre-tests were inadequate for defining the strongest Bacillus production strain.
To overcome the shortcomings of growing Bacillus spec. in batch cultures, Dr. Morabbi Heravi decided to install the Liquid Injection System (LIS) and induce a fed-batch process in shake flasks. 3 mL of a 50% glucose solution was fed in several shots over a defined period, providing the cells with fresh substrate regularly and thereby avoiding the extensive metabolism with high initial substrate concentrations. Undesirable effects like by-product formation were prevented and the initiation of the stationary growth phase was delayed by the constant re-introduction of fresh substrate.
Results
LIS enabled a continuous addition of a 50% glucose solution to the shake flask culture which would not be manageable with a non-automated process (manual handling). When compared with a culture in which the same amount of glucose (3 mL) was fed at one time point, it became clear that the fed-batch process was beneficial for cell viability and the strains growth behavior. Cell lysis could be avoided and biomass levels (monitored with the Cell Growth Quantifier) were increased compared to the single shot feeding.
Besides an improved growth behaviour, the LIS facilitated fed-batch process also showed a significant increase in active protein yields. When compared with the culture in which 3 mL of 50% glucose were fed at once, the fed-batch feeding of 50% glucose to the medium augmented the final protein yield by approximately 30%.
This underlines the importance of culture conditions on the final product yields. Implementing the preferred cultivation conditions early on (e.g., when screening for the strongest production strain in shake flasks) is therefore essential for obtaining consistent results. Only then, the conclusions drawn can be reliably transferred to larger scales, in which fed-batch procedures are the norm for many protein production processes.
The Conclusion
Overall, by enabling fed-batch processes in shake flasks, the LIS contributes to creating bioreactor-like conditions in shake flasks, increasing the reproducibility of results from experiments undertaken in these two systems. By using the LIS, Dr. Morabbi Heravi could characterize production strains in smaller scales, instead of having to use larger scale bioreactor systems, and by this he could save money and time during upstream processing.
Want Results Like These?
We will work with you on a solution that works best for your application.
Testimonial
"I could see that the behavior of Bacillus strains was different in batch cultures compared to fed-batch cultures. By using the LIS, I can now continuously feed glucose in shake flasks. This improves the transferability of results from shake flask experiments to bioreactor runs and widens the application area of this small-scale vessel type, e.g., to determine the best production strains."
- Dr. Kambiz Morabbi Heravi, Project Manager Strain Engineering at Clariant
From Estimation To High-Resolution Growth Curves
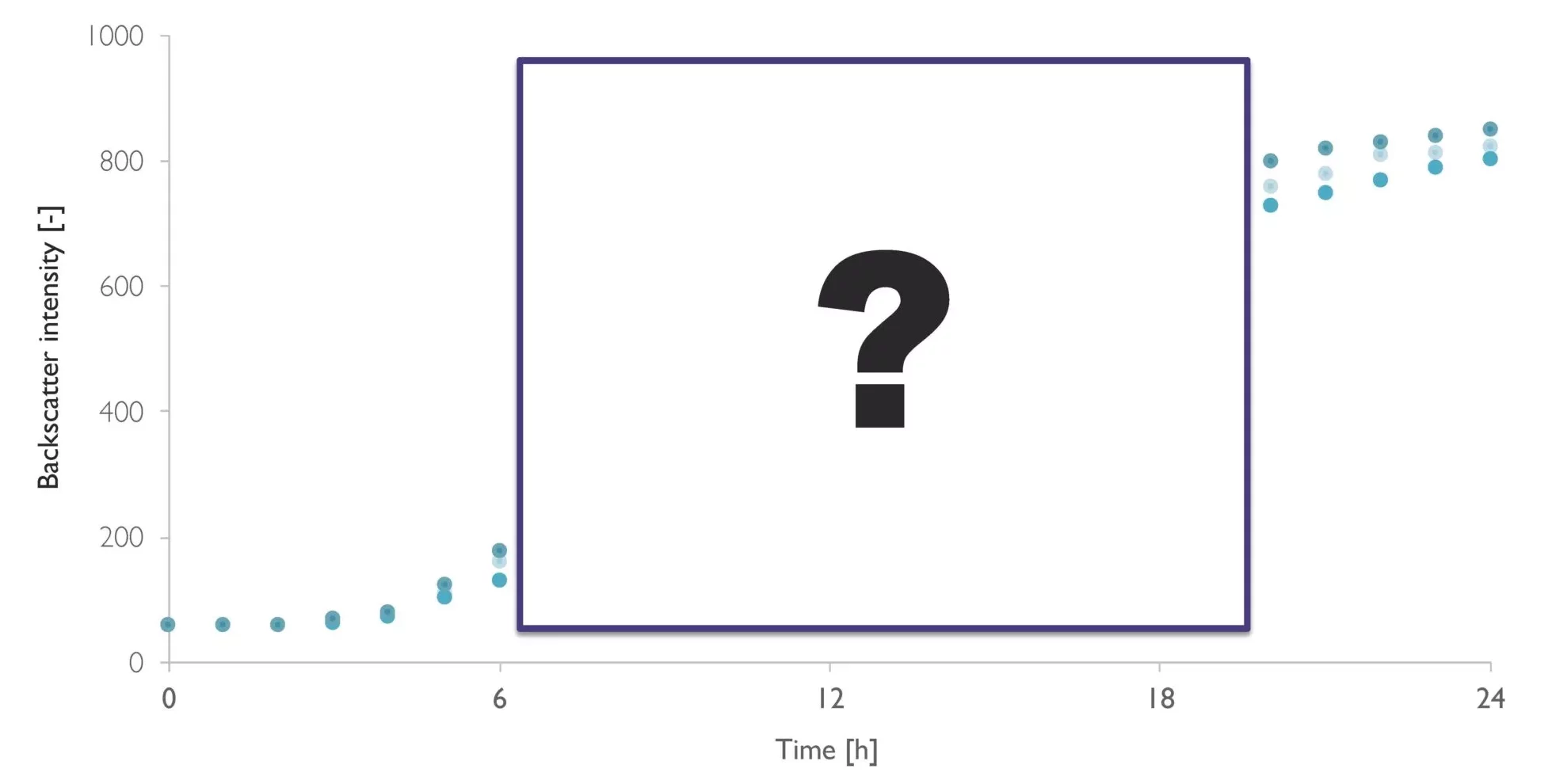
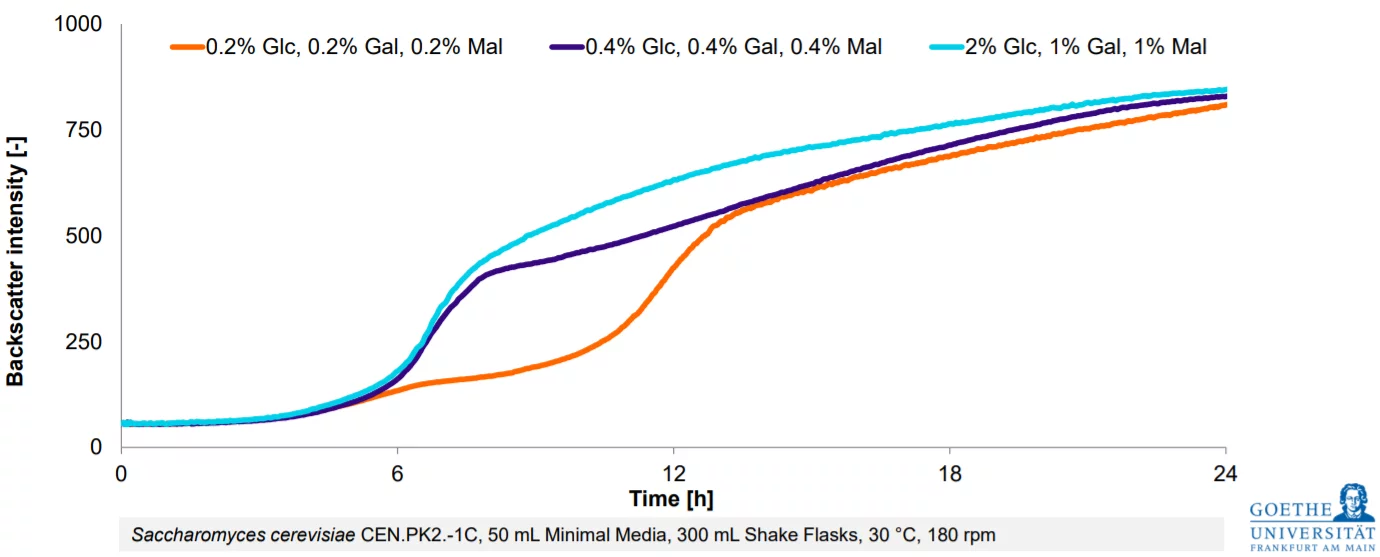
Customer Success Stories
.png)
-Kitana Manivone Kaiphanliam (Washington State University)
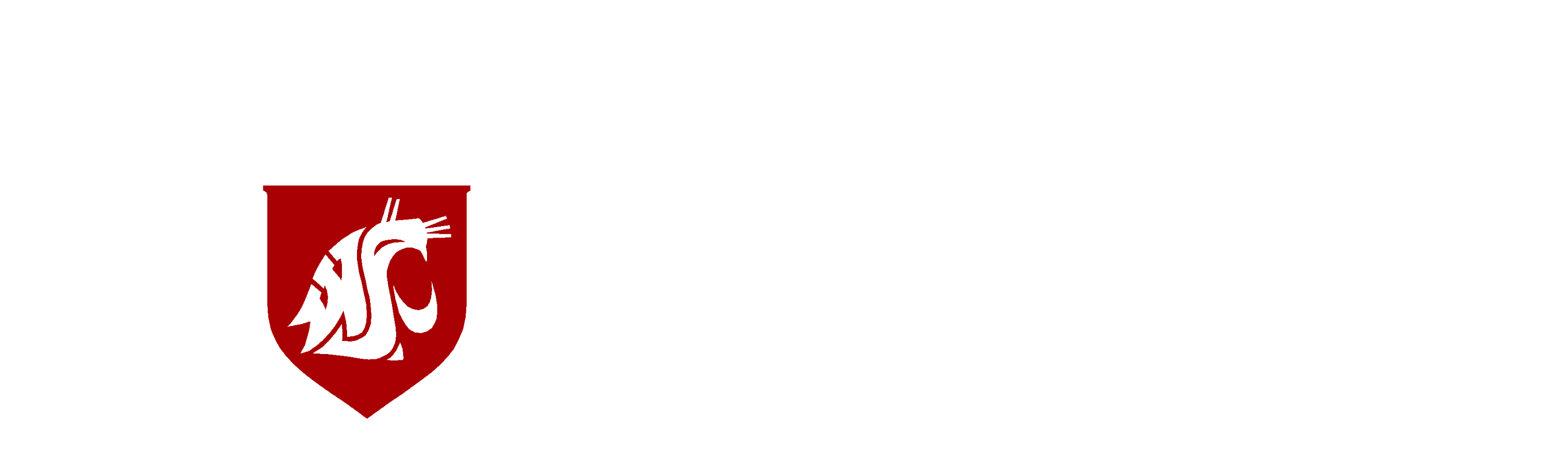